

The Sherline never skipped when using 300 oz-in steppers and the steppers were direct mounted. Another consideration will be how much holding torque will be available. The X resolution is fine but doing a reduction makes the mounting somewhat more complex. I choose to do a 2:1 pulley reduction on the Z because I wanted more torque delivered while cutting threads. To increase the Z axis velocity later after testing.Ĥmm x 0.0394 mm/inch =. Note that the mounting plate will be such that the pulley ratio can be changed as I may want STEPPER x MICRO STEPS x SCREW PITCH x PULLEY REDUCTION = STEPS / UNITĢ00 Steps / rev X 10 X 5.0761 = 20304 STEPS / UNIT 197” / revolution ( 1/0.197 = 5.0761 PITCH ) along with a 2:1 pulley reduction Here are a steps per unit calcs and a look at resolution:ĥmm x 0.0394 mm/inch =. Steppers will be used since the existing controller is for steppers, is portable, and is used for other CNC machines. One important criteria will be resolution ( just how small of an axis move can be made). You are somewhat limited on a conversion as to what will fit and yet the basic mechanical integrity for supporting them is very important. The X axis will use a 12mm diameter x 4mmm screw. The Z axis will use a 16mm diameter x 5MM ball screw. You can do all kinds of calculations for the ball screws, but practically speaking, experience on sizing and mounting from past experience is all that is needed for this conversion. The intent is to minimize the backlash ( you never have zero but you can try ). Both the ball screws are easily adjustable for backlash. ½ HP x 7.35 = 3.7 HP ( approx ) which is a significant HP increase ( > 12X ) as compared to the Sherline. When the backgears are in use there is a considerable increase on torque delivered to the spindle. M pulley S pulley SPINDLE BACK GEAR APPROX Here’s a look at some of the Atlas lathe speeds. You can calculate the HP requirements but the calc’s can be somewhat subjective, and if the motor is marginal, you really don’t know how it will behave under load and the resulting small rpm changes.
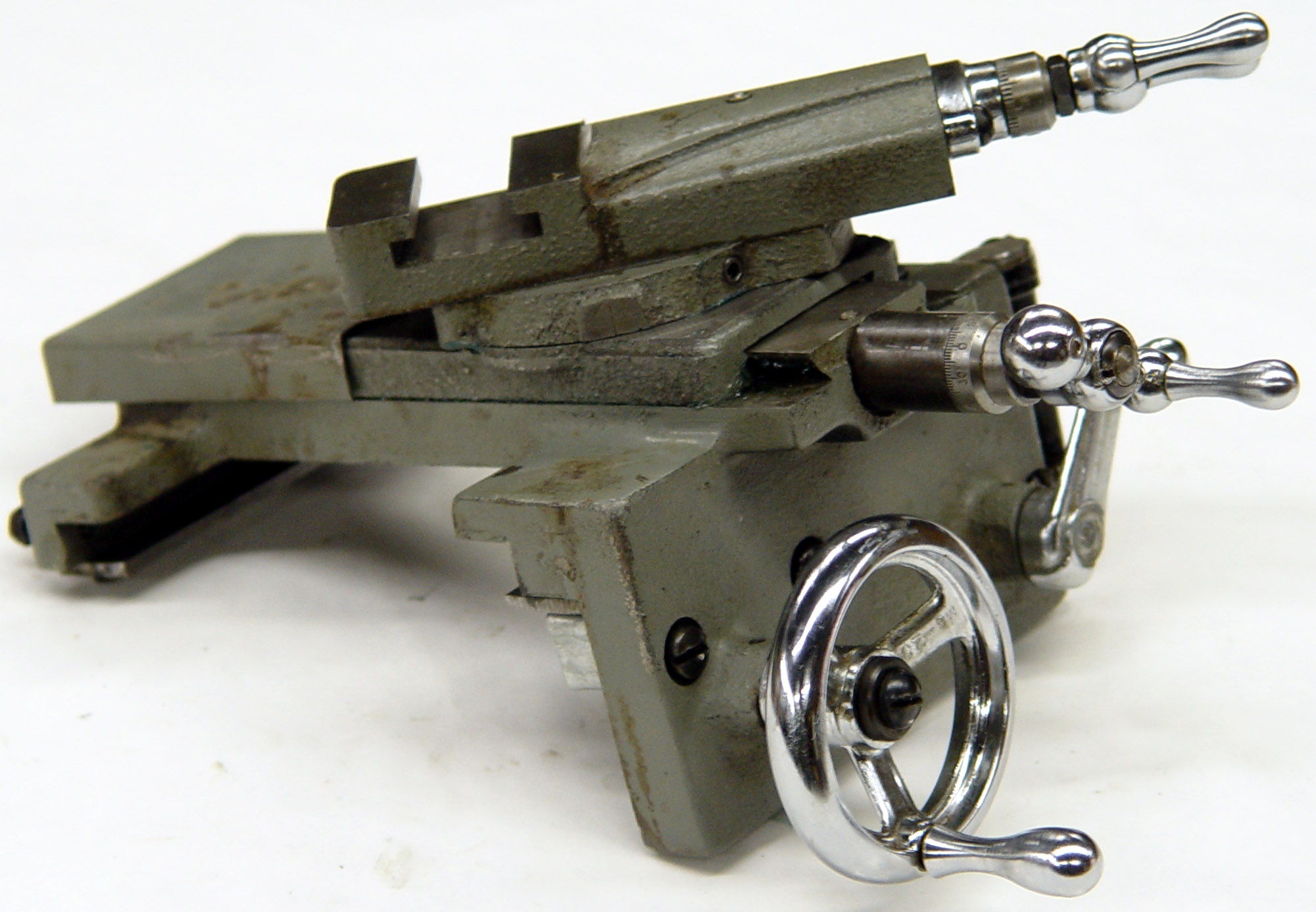
I will probably be making comparisons to the Sherline from time to time. Regular turning on the Sherline was not a problem, but the lack of HP at the spindle during threading left something to be desired. This was one of my dislikes with the Sherline lathe. It’s very desirable to have a constant spindle speed for threading. I will first try the AC motor since backgears can be easily engaged for threading and heavier work. An option would be to use an existing VFD with a 1 HP DC motor.

The following are just some preliminary considerations for the conversion.Ĭurrently a ½ HP / 1725 motor is mounted for use.
